Course Description
Format: Live Online Virtual Training
Date: August 7, 2025
- Thursday, August 7 – 12:00-4:00pm ET
Reg. Deadline: July 24, 2025
Registration Rates
Member
Early Bird*/Standard
$350/$375
Non-Member
Early Bird*/Standard
*Rate ends 6/26/25
$450/$475
Design Basics of Spur and Helical Gears
Learn how to develop and understand customer gear drive application specifications and target performance expectations. Review, calculate and select basic gear terminology variables and design parameters which define tooth bending and contact rating safety factors on two real-life examples. Learn how to optimize gear fatigue Safety Factors for a given target design life and fit new gear designs and ratios into existing center distance using profile shift. Use commercially available software to develop gear geometry factors, calculate and optimize gear set power density and performance. Review common gear failure modes if the design or final accuracy does not meet application requirements. Discuss time and cost of more than 20 other gear drive component functions and drive development steps through prototypes to shipment of compliant assembled production drives. There will be an opportunity to discuss gear design challenges which may be unique to participant industries.
This course is online. A webcam on your computer equipped with a microphone and speakers/headset are required for participation. Space is limited to 20-25 participants per course. Course materials will be mailed in hard copy. Please make sure to indicate your preferred mailing address in the registration process.
How Many CEUs Will I Earn?
As an IACET-accredited provider, AGMA offers 0.3 CEUs for this class.
Learning Objectives
- Discuss aspects of gear tooth fatigue loading and typical failure modes as a basis for gear designs which exceed target design fatigue life
- Understand the various form of drive loads:
- Prime movers and suggested Safety Factors
- Constant load applications
- Variable load/duty cycle applications
- Ability to start with customer supplied gear drive application specification and develop an optimized gear design which meets or exceeds application and performance requirements
- Review gear geometry terminology and design optimization variables beyond information available in Machineryโs Handbook, apply optimization tools currently used in industry:
- Basic Normal Plane Geometry factors โ NDP, NPA, Helix Angle, Tooth Size
- Transverse Rolling Plane Performance variables โ Profile Shift, Material, Heat Treatment, Accuracy, High Contact Ratio gear geometry and efficiency
- Rating factors โ Tooth Bending S. F., Tooth Contact S. F., Micro Pitting S. F.
- Additional performance enhancing processes โ shot peen, isotropic finishing
- Calculate contact and bending Safety Factors as (Material and Design allowable loads) divided by (application loads) for a target design life.
- Learn how to fit a new gear ratio into existing housing and center distance using profile shift
- This course is focused on gear design, but reviews functionality of over 20 related drive components and design related processes.
- Apply design tools and gear performance enhancements to optimize:
- Rating
- Operating noise level
- Efficiency
- Gear mesh contact
- Lubrication
- Discuss gear drive design process steps, time, and costs from receipt of customer application specifications through design, prototype development/testing to manufacturing and shipping production units which meet or exceed customer expectations
- Work through two real life examples, (pre-defined), developing optimized spur and helical gear sets which exceed customer application specifications. The trainer does not have and active license for KISSsoft and cannot work through examples โliveโ
Are you a member of the American Bearing Manufacturers Association (ABMA)? As an ABMA member, you receive discounts on all programs that AGMA offers. Email AGMA Education at education@agma.org for a complimentary promo code to receive member pricing on this course.
Instructors
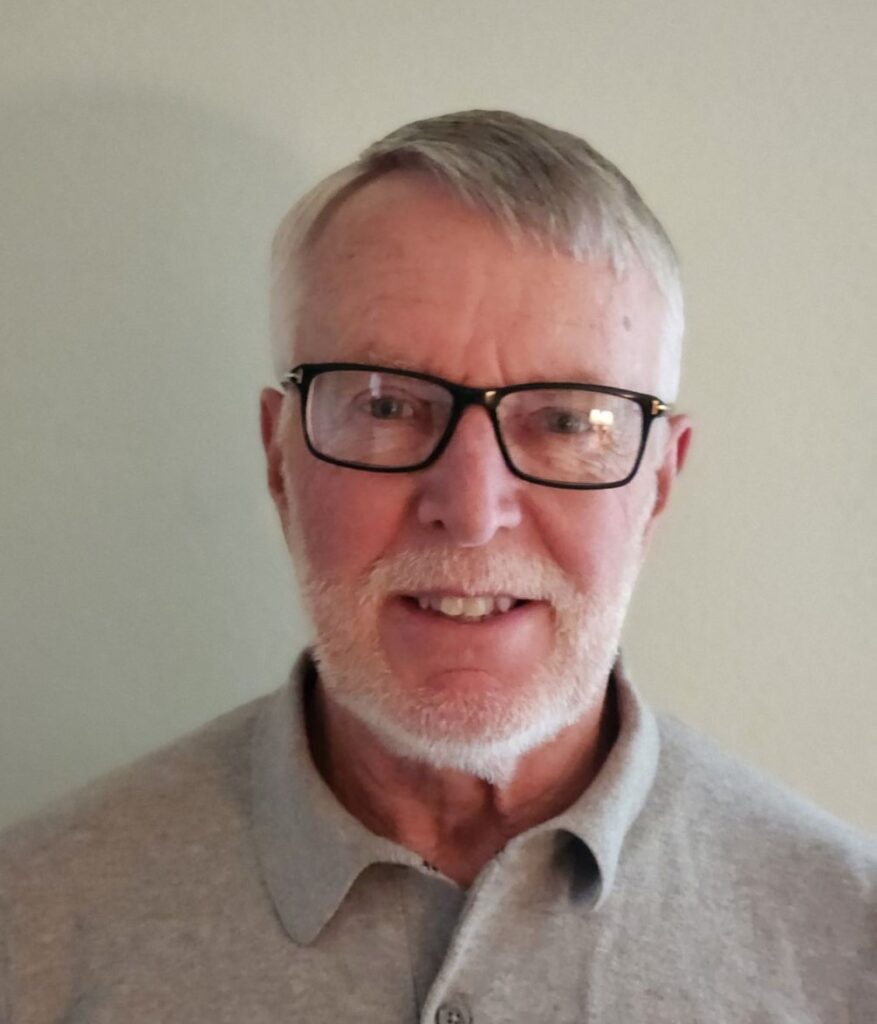
TERRY KLAVES
Terry Klaves semi-retired from the Milwaukee Gear Division of Regal Beloit in 2017 after 45 years of work in the gearing industry with four different companies, positions varying from gear engineer to VP of Engineering and responsibilities including gear design, optimization, manufacturing and Quality Assurance. He has a passion for solving gearing related problems and continues to serve the gearing industry as part time consultant and trainer for AGMA, in addition, he is Chairman of the AGMA TC-60 Committee, contributing to development of ISO gearing standards. Terry graduated with a BS-Engineering in 1976 and a MS-Engineering from UW-Milwaukee in 1981 and enjoys sharing his knowledge and passion for gears through formal consulting and training activities.
Photo Release
From time to time AGMA uses photographs, survey answers and testimonial of AGMA events in its promotional materials. Unless this permission is revoked in writing to the AGMA, by virtue of your attendance all attendees agree to the use of their likeness in such materials.
Cancellation and Payment Policy
Please view our cancellation policy.
Please view our late registration policy.
Please view our code of conduct.