Course Description
Format: Live Online Virtual Training
Date: November 12-13 & 19-20, 2024
- Tuesday, November 12 – 12:00pm-4:00pm ET
- Wednesday, November 13 – 12:00pm-4:00pm ET
- Tuesday, November 19 – 12:00pm-4:00pm ET
- Wednesday, November 20 – 12:00pm-4:00pm ET
Reg. Deadline: November 4, 2024
Gear Systems Design for Minimum Noise
The need for noise control and its relation to gear drive design will be discussed. The general nature of noise and its measurement will be examined, with particular emphasis on terminology standards, and units of measurement appropriate to gear technology. Gear noise, per se, is seldom heard by and observer. The mechanism by which observer noticed noise is generated and transmitted will be defined, described, discussed. Before attempting to solve a noise problem with an existing unit or beginning the design of a new unit, the nature of the noise must be defined. Both experimental and analytical methods will be covered, with particular emphasis on application rather than theory.The many factors that influence the noise produced by a gear system will be discussed. The relative effects of each factor will be studied qualitatively. Factors to be considered include gear tooth geometry and accuracy, speed, materials, housing design, bearing type, gear type, air entrapment, root clearance, interference alignment, surface finish, and phasing. Although, ideally, the designer should solve noise problems on the drawing board, in the real world this sometimes does not occur. Various techniques that can reduce the noise level of existing gear systems without requiring major hardware replacement will be presented and discussed. Included in the discussion will be enclosures, absorbers, dissipative dampers, isolators (gearbox and gear blank), and impulse phasing.
Registration Rates
Member Rates
First Registrant per Member Company
$1,250
Additional Registrant per Member Company
$1,050
NON-MEMBER RATE
First Registrant per Non-Member Company
$1,750
Additional Registrant per Non-Member Company
$1,550
How Many CEUs Will I Earn?
As an IACET-accredited provider, AGMA offers 1.3 CEUs for this class.
Learning Objectives
- Understand the need for gearbox system noise control and, especially, the difference between โgear noiseโ and โgearbox system noiseโ.
- Become familiar with the โnatureโ of noise and its measurement as well as terminology standards, and units of measurement appropriate to gear technology.
- Learn the mechanisms by which observer noticed noise is generated and transmitted.
- Gain a knowledge of the experimental and analytical methods for measuring noise, with particular emphasis on application rather than theory.
- Explain the importance of equal planet/star gear spacing and how a system can be designed with unequal planet spacing.
- Understand the various design and manufacturing factors that influence gear system noise including gear tooth geometry and accuracy, speed, materials, housing design, bearing type, gear type, air entrapment, root clearance, interference alignment, surface finish, and phasing.
- Recognizing that it is often necessary to address noise issues after the gearbox system is designed, learn how enclosures, absorbers, dissipative dampers, isolators (gearbox and gear blank), and impulse phasing can be applied to existing systems to reduce noise level.
Who Should Attend
Gear and gearbox design and quality control engineers involved with design and manufacture of gear systems used in applications where noise is of special concern such as medical equipment, electric vehicles, and any other application where the level and/or character of the noise emitted by the gear system is of significant concern.
Are you a member of the American Bearing Manufacturers Association (ABMA)? As an ABMA member, you receive discounts on all programs that AGMA offers. Email AGMA Education at education@agma.org for a complimentary promo code to receive member pricing on this course.
Instructors
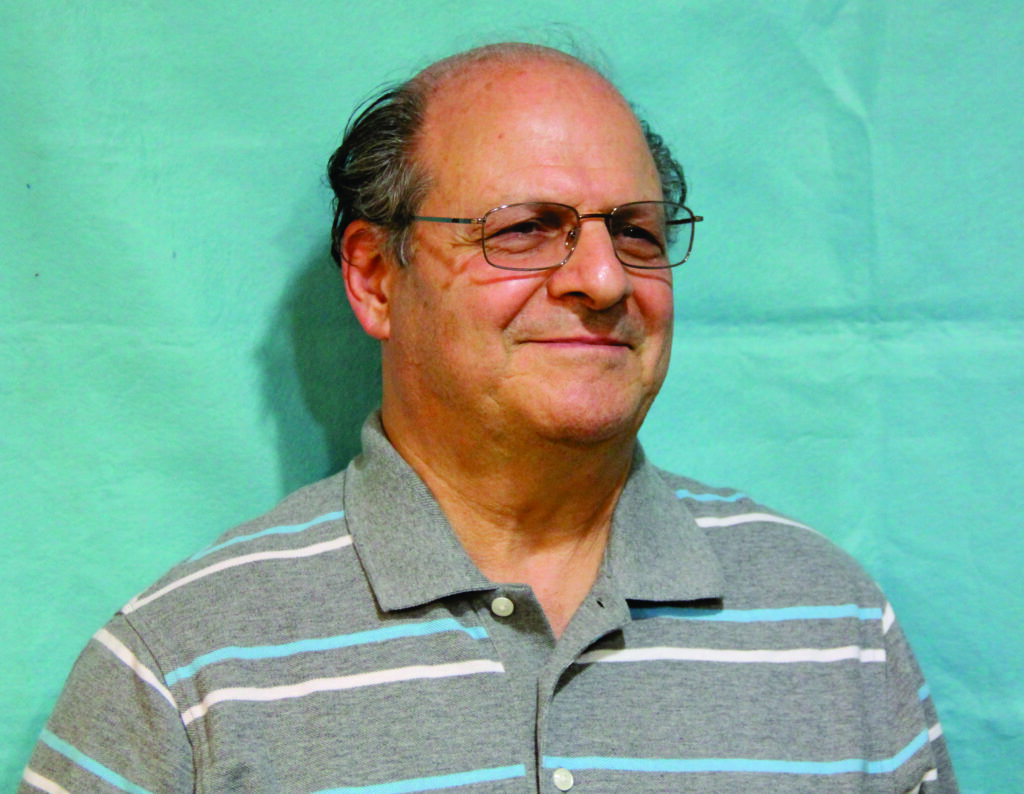
Raymond J. Drago, P.E.
Raymond J. Drago is Chief Engineer of Drive Systems Technology, Inc. (DST), a mechanical power transmission consulting organization that he founded in 1976. Mr. Drago also worked for the Boeing Company โ Helicopters Division until his retirement after 37 years of service. Currently Mr. Drago is involved in the analysis, design, manufacture, assembly, and testing of many gear systems. In his role with DST, Mr. Drago is active in all areas of mechanical power transmission, including the design and analysis of drive systems in a very diverse field of application from heart pumps to very large mining & mill gears. He has used his 58 years of gear technology experience to prepare and deliver more than 150 Technical Papers and 385 courses dealing with various aspects of gear design and analysis.
I started working at Boeing in 1967 and continued until my retirement in 2004. I started Drive Systems Technology in 1976 as a part time activity while still working at Boeing (with Boeingโs knowledge and approval, under strict guidelines) which eventually grew to the point where I retired early from Boeing in order to pursue DST as a full-time activity.
Photo Release
From time to time AGMA uses photographs, survey answers and testimonial of AGMA events in its promotional materials. Unless this permission is revoked in writing to the AGMA, by virtue of your attendance all attendees agree to the use of their likeness in such materials.
Cancellation and Payment Policy
Please view our cancellation policy.
Please view our code of conduct.